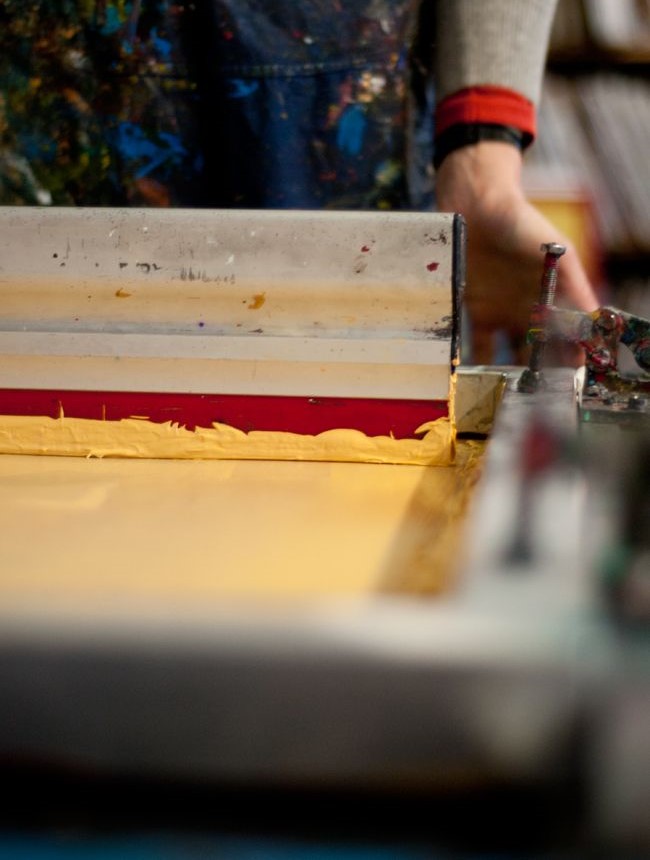
What is Silk Screen Printing Process? Complete Step-by-Step Guide.
The silk screen printing process, also known as serigraphy, is a versatile and modern method of transferring images, designs, and patterns onto various surfaces with precision and accuracy. This centuries-old printing technique has evolved into a modern art form and is also a highly effective industrial process.
History
Ancient China was the place where the silk screen printing process or serigraphy originated, and it was initially used for printing intricate designs on fabric, primarily silk. The silk screen printing process remained a well-kept secret for centuries until it gradually spread to other parts of Asia and Europe. It became prominent during the 18th century as a means of printing on various materials, including paper and textiles.
However, the silk screen printing process as we know it today truly blossomed during the 20th century. It gained immense popularity in the United States in the early 1900s, significantly during World War II when it became a vital method for printing flags and other military materials. After the war, screen printing continued to evolve and expand its range of applications, including textiles, graphic arts, and industrial printing, thanks to artists and innovators who recognized its potential for artistic expression, revolutionizing the way we view the technique.
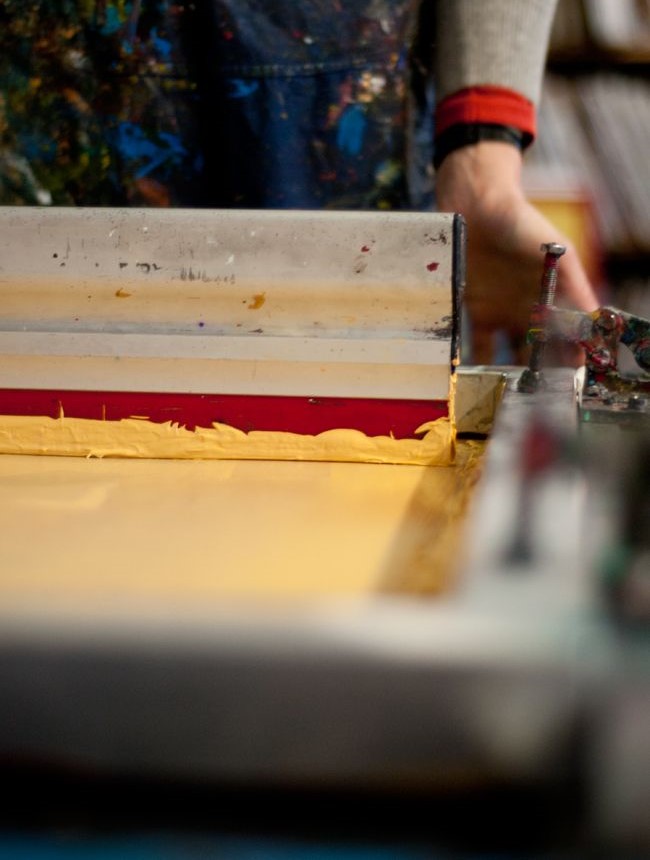
The step-by-step Screen Printing Process
Preparing the Silk Screen
To begin the silkscreen printing process, you create a screen, traditionally using silk, although modern screens often use polyester or nylon mesh. You stretch the screen tightly from all four sides over a wooden frame, and then you create a stencil on it to define the design that you will print.
Exposing the Emulsion
The acetate sheet features the design, and we place it onto the emulsion-coated silk screen. We then direct very bright light onto the entire setup. The light causes the emulsion to harden, leaving the areas of the silk screen covered by the design in a liquid state.
Creating a Stencil
After the screen has been exposed for a set time, the areas of the screen not covered by the design will have turned hard. Any unhardened emulsion is then carefully rinsed away. This leaves a clear imprint of the design on the screen and is now left with a completed stencil ready to be used for printing.
Ink Application
Once the screen is prepared, ink is applied to one end of the screen. A squeegee, a tool, is used to press the ink through the stencil and onto the surface below. The areas where the emulsion is hardened block the ink from passing through where the design is not intended.
Printing
The surface, which can be fabric, paper, plastic, or other materials, is placed under the screen. The squeegee is then pulled across the screen, forcing the ink through the stencil and onto the desired surface. This process can be repeated for multiple colors, with each color requiring a separate screen.
Benefits of Screen Printing
The Silk Screen printing technique is a versatile and widely used printing process with several major advantages.
Versatility
You can use the silk screen printing process on a wide range of materials, including paper, fabric, plastic, glass, metal, and wood. The versatility of this technique makes it suitable for various applications, from apparel and posters to signage and promotional products.
Durability
Silk screen-printed designs are highly durable and long-lasting. The ink used in this printing method is thicker and more reliable than other printing methods, making it resistant to fading, cracking, and washing away.
Consistency
The silk screen printing process provides consistent results across multiple copies, ensuring uniformity in all final products.
Customization
Silk screen printing allows for a wide range of customization and personalization by creating unique designs and prints for specific art or events.
Vibrant Colors
This printing technique allows the artist to use vibrant and opaque ink colors. The ink can be applied in a single vibrant color or a single layer but is often applied in multiple layers, resulting in rich and bold designs with high color saturation.
Screen Printing Techniques & Applications
There are different types of screen printing techniques, and understanding the different techniques can provide different results.
Spot Color Printing
The most widely used printing technique is spot color screen printing. A stencil pushes the ink through the mesh, creating a vivid, solid spot of color.
Halftone Printing
Halftone printing works with single colors in gradients. By using a single ink color and employing half-toning, this technique creates various shades when viewed from a distance. Just like the aquatint technique of printmaking, it gives a tonal effect. It is also an efficient method to achieve a multi-colour appearance without added complexity.
Grayscale Printing
Grayscale printing is a go-to method for rendering full-color images using only shades of grey or halftones. The more dots in the halftone, the greater the detail in the print. This technique also extracts color scales, such as CMY or RGB, in grayscale.
Duotone Printing
Duotone screen printing combines two halftones to reproduce an image with two colors. It starts with a black halftone printed in black ink, followed by another halftone in colored ink. This technique is similar to sepia-toned photography and imparts a sophisticated and artistic touch to your prints.
CMYK 4 Colored SilkScreen Print
CMYK, or four-colored printing, represents the pinnacle of complexity in printing. It blends the four primary ink colors (CMYK, which stands for cyan, magenta, yellow, and key (black)) to generate the desired color tones. While it can be done manually, automatic methods are also preferred for optimal results. CMYK allows for a wide spectrum of colors, making it a versatile choice for vibrant and intricate designs.
T-Shirt Silk Screen Printing
Manual printing on fabric is a time-honoured art form that continues to captivate and inspire creative artists worldwide. Its rich history, effective process, and ability to produce enduring and vibrant designs make it a valuable tool for artists, designers, and enthusiasts. Whether you’re looking to create custom apparel, unique home decor, or striking pieces of art, silk screen printing on fabric offers a canvas of endless possibilities for unlocking your creative potential.
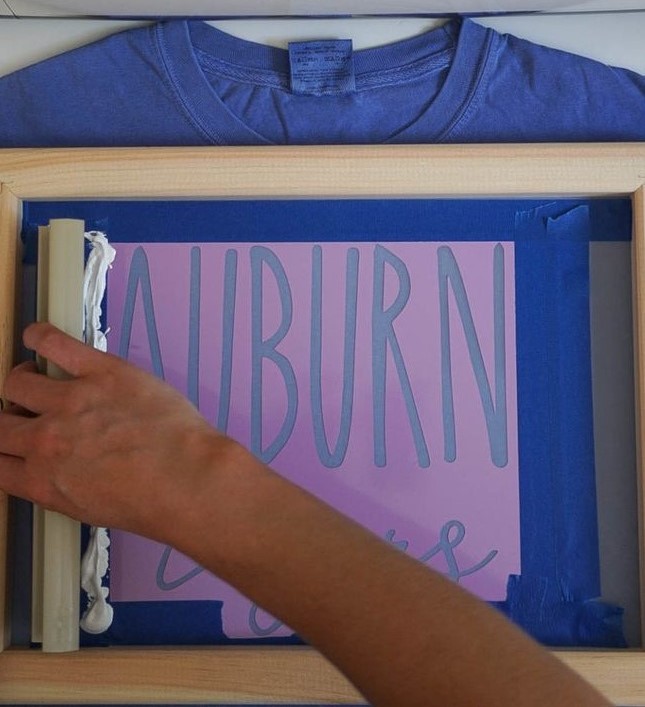
The silk screen printing process continues to be a popular method for creating custom designs. Screen printing shirts, textiles and fabrics. Here are some of its contemporary applications.
Fashion
Designers and clothing brands use it to create unique and visually striking patterns on garments t-shirt screen printing, dresses, and hoodies.
Home Furnishings
The silk screen printing process allows manufacturers to create decorative pillows, curtains, and table linens, giving homeowners the opportunity to infuse their spaces with personal style.
Promotional Items
Businesses use this technique for custom promotional products, including tote bags, caps, and promotional banners.
Custom Merchandise
Individuals and small businesses turn to this method of printing to produce custom merchandise, like personalized clothing, accessories, and gifts.
Screen Printing on Paper
Screen printing on paper or card is similar to printing on fabric. Whether it’s through the careful layering of colors or the quality of the print, this process of printing on paper offers artists a unique and rewarding creative experience that always stands out. It offers high-quality printing because it uses thicker ink compared to other printing methods. Thicker inks allow for more solid and vibrant color application, enabling you to create bolder, more eye-catching, and more colorful designs that can be seen from even far away.
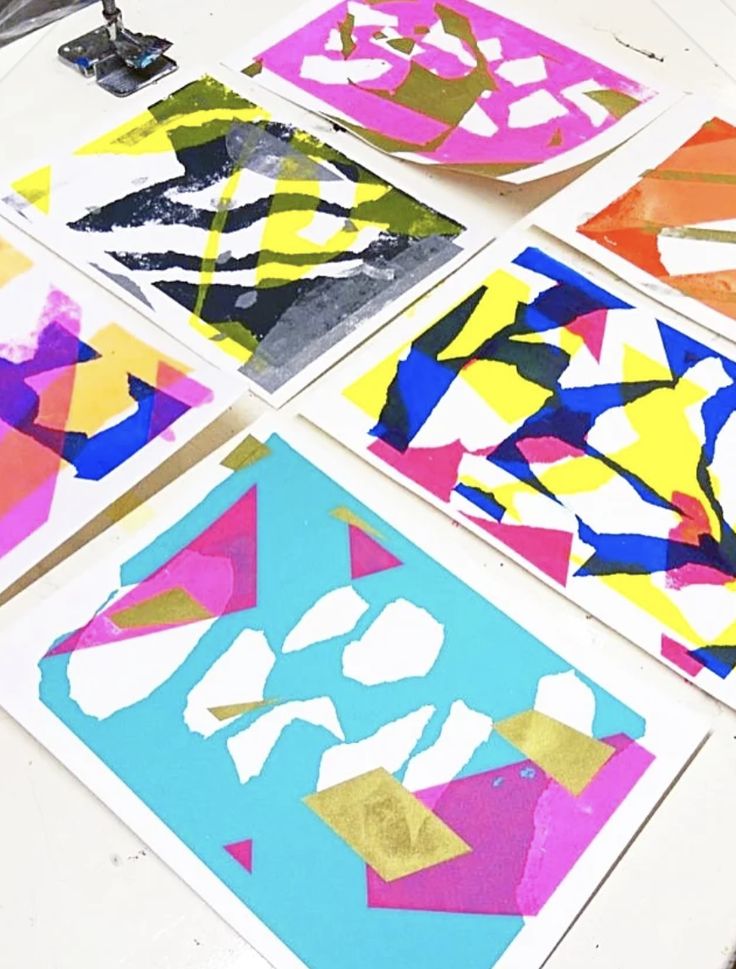